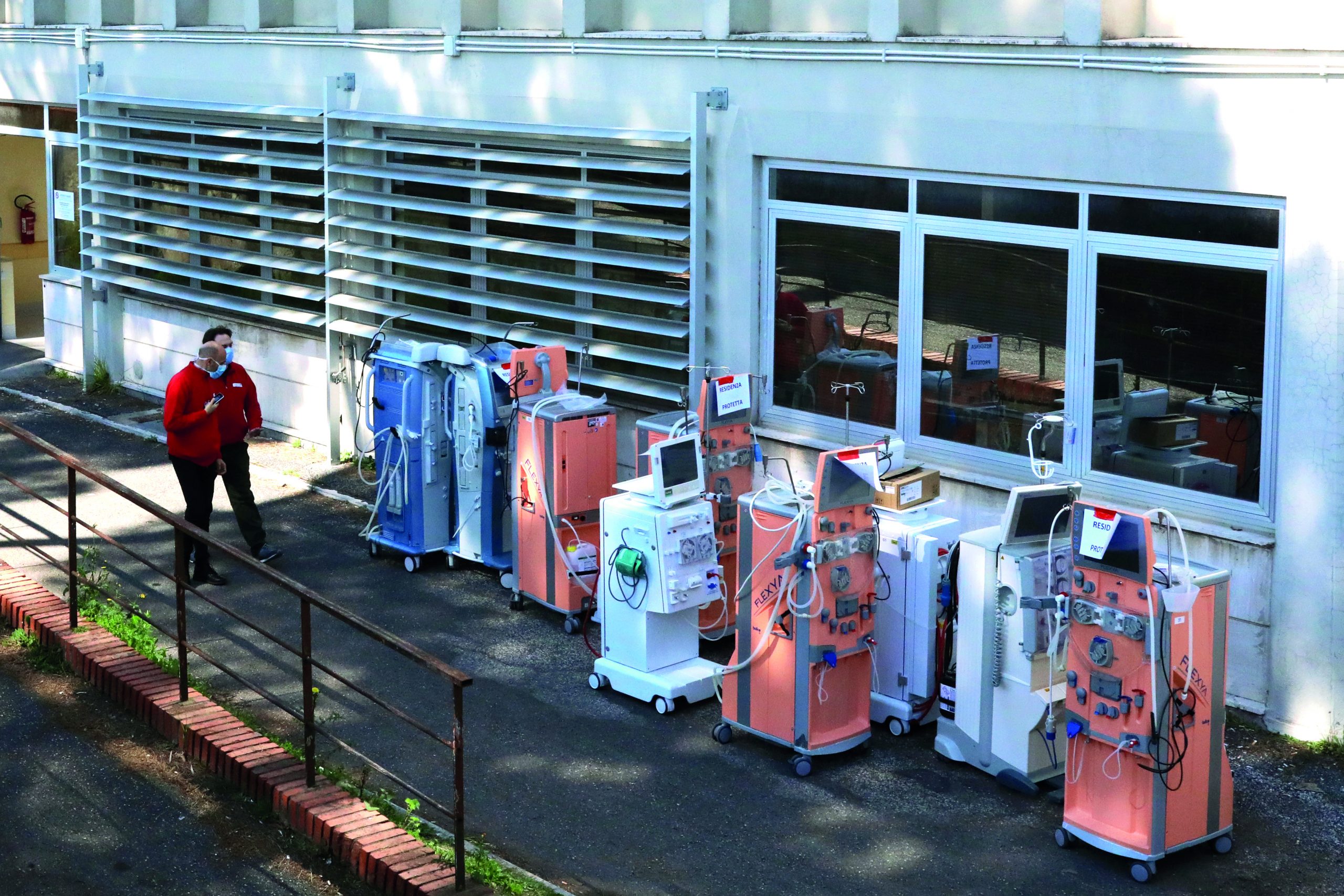
For the NHS to cope with the Covid-19 pandemic, Britain urgently needs more ventilators. The government has called for the private sector to help increase the stockpile of this critical piece of medical equipment. Professor David Delpy, fellow of the Royal Academy of Engineering, answers questions on the logistics of meeting the challenge.
The government has asked UK manufacturers to turn their hands to the production and assembly of ventilators, the number of which in circulation in the NHS is reported to be as low as 5,000. What are the challenges of the manufacturing industry switching assembly lines?
This should not be a problem for most of industry, so long as they have full specifications for the items to be produced and there is no need for materials that may not be standard stock. Ventilators will generally be hand-assembled from components, many of which can be made on more automated manufacturing lines. Note, however, that many modern ventilators contain specialist sensors and controllers – for example gas flow valves, gas mixers, pressure, and gas concentration sensors – which may be bought in from specialist suppliers outside the UK.
Supply of these may be the limiting factor in ramping up production. Specialist medical engineering knowledge or staff with specific skills are not required to make the components themselves, though knowledge of the relevant regulations will be needed in specifying these and in final manufacture and assembly. The skills needed for many complex industrial engineering products are transferable to medical technology.
In theory, could any manufacturer do it?
This depends on the type of ventilator being made. Producing modern high-tech ventilators requires a mix of skills as they contain electronic, mechanical, software and plastic or rubber-moulded components and sensors. The larger companies that have already responded to the government’s call to manufacture ventilators, such as Rolls Royce, JCB, Unipart and Dyson, have all the necessary skills either internally or through their supply chains, so long as any specialist components, sensors or materials are available.
If the decision was to make some of the older-style mechanical ventilators, the components for these can be manufactured by most engineering companies with standard machine tools and moulding or injection equipment. Note that all ventilators involve the use of some “single use” or “disposable” items. These include plastic connecting tubing, intubation tubing, mouthpieces and so on, which are replaced for each patient. These are all supplied sterilised. There will be a need to significantly increase production of these components, as well as the numbers of ventilators in the system.
What is the risk of manufacturers cutting corners, and will ventilators be subject to testing or regulation?
The risks should be minimal as existing ventilator manufacturers and other major engineering companies have a well-specified manufacturing specification and quality assurance system. One potential problem that could – but hopefully won’t – arise is if there are specific components or elements, such as gas sensors, from overseas suppliers who may not be able to supply them, either because of supply-chain disruption or demand from other countries with the same ventilator problem.
These items have usually been specifically manufactured, tested and regulated. It may be possible to find alternatives, but obtaining approval usually takes at least a year, so some emergency exemption would be required if they were to be substituted.
Realistically, how quickly can the UK manufacture the number of ventilators it needs?
Assuming there are no supply constraints for the basic materials and components, which is certainly the case for mechanical ventilators, a switch over to manufacture should be very quick – my guess is around a week. For mechanical ventilators, many components could be produced by several suppliers, so the main constraint is likely to be assembly and testing.
How much cleaning and maintenance do ventilators need once they are in the system, and how much of a strain could that be on the NHS?
This is key. The ventilators will need a large supply of “single use or disposable” components. Additionally, between each patient use, ventilators have to be stripped, cleaned, reassembled and sterilised. This is most frequently done in hospitals by skilled technicians in clinical engineering or medical physics departments. The increased workload may not be sustainable with current staff numbers. This is another reason for perhaps considering simpler mechanical ventilators, and is a strong argument for limiting the new ventilator supply to one or two designs. The last thing we need is six different designs for which people have to be trained, and which use different components. Interchangeable parts should be the rule.